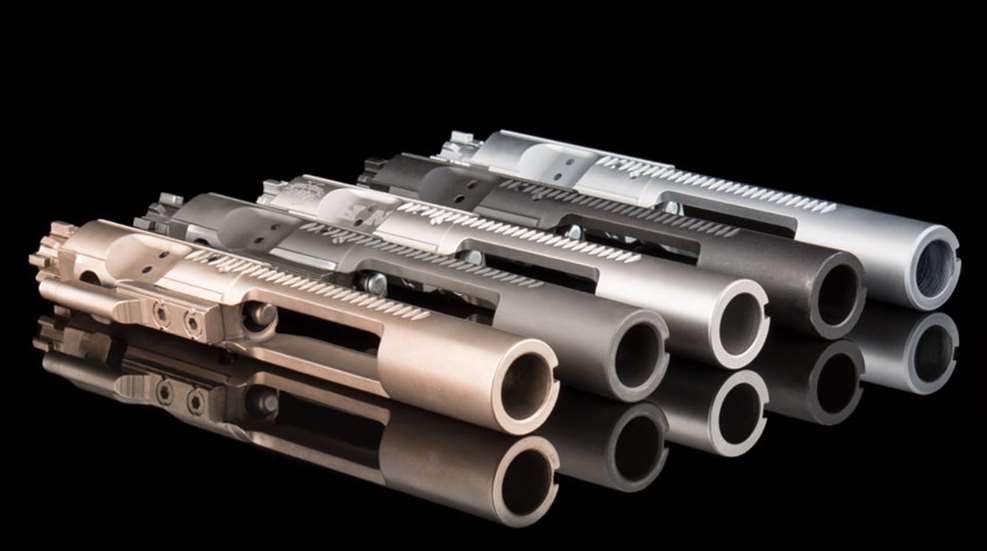
Bolt-carrier groups above, from left, represent Nickel Boron, phosphate (Palmetto State Armory), Robar NP3, black nitride (Brownells) and chrome-plate (Daniel Defense).
Advances in gun coating technology can be wonderful. Back when I was knocking around the woods of my youth, I carried wood-stocked rifles with steel that was either blued or color-case hardened—and usually with a bit of surface rust around the margins. Most of the [few] commercially available modern sporting rifles and surplus longarms of the day had some form of Parkerized finish. The only other option I was aware of at the time was bright stainless steel. But, those firearms were too shiny for my liking (and out of my price range anyway). The standard-issue guns I later carried in the Army were all Parkerized. I swear they began turning rust-orange as soon as I looked away unless they were slathered with CLP. Internal components in those days were usually stainless, Parkerized, blued or sometimes left “in the white.”
Today we have much better gun coating options for our ferrous-metal rifle parts. Each has its pros and cons, but all provide better protection from the elements than the coats of old. Here are some alternatives to the buffed blue and phosphated-gray rust magnets of days gone by.
Plated
Reflective, plated finishes such as hard chrome, nickel and gold have been around longer than anyone presently reading this magazine. While no longer popular on long gun exteriors, surface treatments like chrome-plating work well on and in certain internal components. Most tactical-rifle shooters have experience with chrome-lined bores, which provide wear- and corrosion-resistance. We also find chrome in less-obvious places like piston-rod ends, the inside of an AR’s bolt carrier and in the open end of the carrier’s gas key. One complication to chrome-plating is that it adds to the dimensions of finished parts, so components must be undersize by whatever thickness the plating will add.
Attempts to chrome-line rifle bores date back to the first half of the 20th century. The process has long since become standard in military and police battle rifles and carbines around the world. Sources for true match-quality, chrome-lined barrels can be counted on one hand, with fingers left over. Most chromed bores are very durable, but they typically come up short in the accuracy department due to variations in thickness throughout the bore. Chrome-plated parts are slicker than bare steel, allowing for easier cleanup of pistons and bolt components. Unfortunately, the constant slamming of metal on metal can cause chrome to wear or flake off of hard-use parts like bolt-locking lugs, which can affect accuracy, reliability and even safety. Chrome plating seems to do its best work inside of components subjected to high friction—but not hard impacts—and when done well, is still a great solution to limit erosion and wear.
Nickel-Boron
Nickel-boron (NiB) is an “electroless” gun coating, instead applied chemically. That makes for extremely uniform surface coatings on parts with tight tolerances, like a trigger’s sear-engagement surfaces. NiB reduces friction and speeds the cooling of high-heat components due to the increased surface area created by the coating’s texture. Internal rifle components appear to be the best-suited for NiB, and in my experience, this gun coating is much more durable than traditional plated finishes on contact surfaces like bolt-locking lugs. NiB provides excellent corrosion resistance, but over time it will give way to the ravages of high heat and pressure on hard-use components. NiB-coated components are relatively easy to clean up but may become discolored when subjected to high heat.
Nitride
Names like Melonite, Ni-Corr, Black nitride or salt bath nitride are all variations of a surface treatment formally known as “Liquid Salt Bath Ferritic Nitrocarburizing Non-Cyanide Bath” (FNC) or simply nitriding. This process isn't really a gun coating, since it doesn’t change a part’s finished dimensions, so it is well-suited for both precision internal components and bores. An added plus is, unlike chrome lining—which is mostly limited to chrome-moly steel blends—nitriding is optimal for stainless-steel bores, too. Its high resistance to wear and corrosion also make it useful as an external surface protectant. Nitrided surfaces are very hard and, since the FNC process transforms the surface rather than coating it, the metal itself must be removed to get through to unprotected steel below. I have been using nitrided barrels, bolts and trigger groups for years and have yet to wear one out. From a production standpoint, nitriding is inexpensive and so long as it is done correctly, the high temperatures that the process relies on for application will not harm steel rifle components.
Spray-on
Gun coatings such as Cerakote, DuraCoat and KG Gunkote are applied via compressed-air sprayers. They differ somewhat in composition and may be air- or heat-cured. Spray-on coatings are best-suited for rifle exteriors where the inevitable variations in thickness will not change tolerances nor impede function. They have a fair amount of wear resistance, but heavy use or careless handling can still cause them to wear through, scratch or chip off. When properly applied, spray-on gun coating provides good corrosion resistance and allow you to truly customize your rifle’s appearance due to endless color and pattern variations. Spray-ons have the added benefit of being equally well-suited for aluminum, polymer and wooden rifle components, too. These finishes are susceptible to harsh chemical strippers like acetone or ammonia-based solvents, so stick to safer cleaners like mineral spirits or conventional powder solvents when cleaning painted rifles.
High-tech gun coatings such as Robar’s NP3 and FailZero’s Exo Technology boast additional advantages over the coatings described here. And you can rest assured that behind-the-scenes work is being done that may well represent a quantum leap in metal surface treatments. But traditional firearm finishes still have their place. A deep, lustrous blued rifle barrel or richly contrasted, color-case hardened receiver combined with hand-rubbed wooden stocks can evoke awe and envy, even today. However, if the nature of your rifle work requires something more practical, aim for components coated with a modern, durable and cost-effective surface treatment.