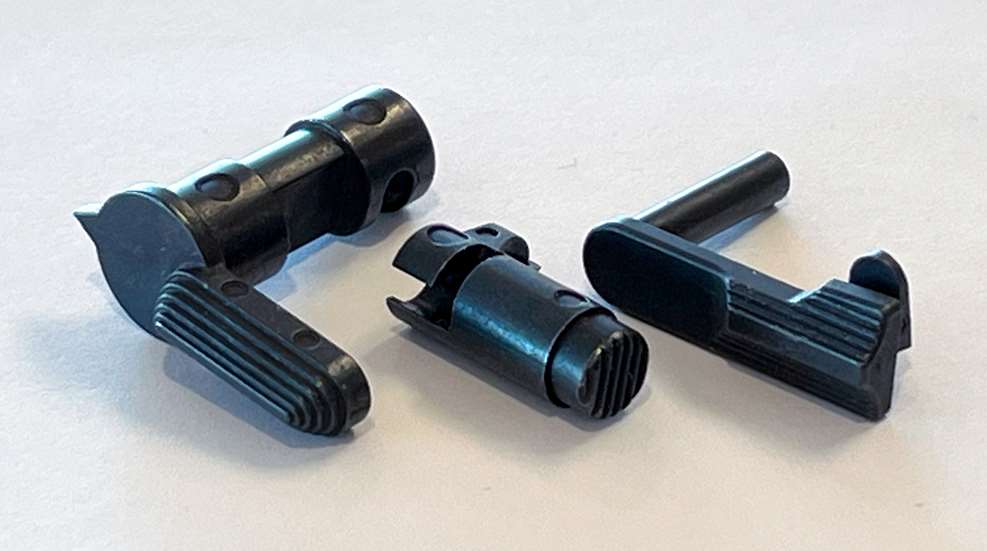
Metal-injection molding (MIM) creates complex, durable and reliable metal parts in things we use daily. Its ability to churn out high volumes at reduced cost endeared it to the firearm industry decades ago. Despite that fact, gun companies we asked about the process were tight lipped. Widespread misconceptions about performance likely caused that silence, but MIM became a hot topic at the 2024 SHOT Show, when Magpul announced it is launching a line of knives this spring. The blades are going to be metal-injection molded.
Edge retention, combined with the ability to avoid chipping and breakage, is traditionally thought to be the exclusive realm of top-quality steel. The company is blazing a new trail, however. “MVN35, the proprietary blade steel developed by Magpul for our upcoming line of knives, is a MIM-produced knife steel on par with the super steels found in today’s premium knives,” an unnamed Magpul representative explained.
Because the knives—produced in partnership with Blade HQ—were not yet available when we asked for more information, the company politely declined to answer. The response was the same when we asked several gunmakers about their reliance on MIM, even though it’s common knowledge many use parts made by the process.
One of the largest manufacturers of MIM parts for the firearm industry, however, did provide some insights. Smith Metal Products makes triggers, hammers, sights, safety levers, firing pins, slide stops, barrel extensions and other parts for several firearm firms. Non-disclosure agreements prevented us from finding out who’s buying.
“Metal-injection molding has helped firearm manufacturers lower the cost of production to make gun owner-ship more affordable without sacrificing quality,” said Todd Jensen, vice president of Smith Metal Products. “Pistol designers use metal-injection molding to design components that would be impossible to make with any other metal-forming technology. It also allows manufacturers to combine multiple components into a single, more compact design, which reduces the weight of the firearm.”
It was during the 1970s that it became widely accepted. “Firearm manufacturers were the early adopters of metal-injection-molding technology, because you can get extremely complex part designs in small metal components,” Jensen said.
Metal powder and a plastic binding compound are mixed. When done it has a thick, clay-like consistency that is squeezed into a mold. With heat generated by that pressure, or applied externally, the binder and metal lock into a solid form. After removal and cooling, that so-called “green” part takes a hot bath in a solvent or goes through catalytic debinding—the process used by Smith Metal Products—to remove the binder. That leaves strength-compromising gaps in the component, so it needs one final step.
To fuse the metal together in one solid part, it is sintered in a furnace. During this process, it shrinks—depending on original mix—as much as 30 percent. Done correctly, the result precisely matches dimensions requested by the gun or knifemaker.
There are a variety of powdered materials that can be used—and combined in different proportions—for the original mix. They include, but are not limited to, stainless steel, tungsten, nickel alloys, some carbides, precious metals and others. The size of their particles can be varied to produce different characteristics in the final product. Five to 20 microns is a common dimension and explains the glass-smooth finish.
“MIM technology has evolved through the years with improvement at every step in the manufacturing process,” Jensen said. “More consistent metal powders, scientific molding processes and tightly controlled sintering furnaces contribute to the success of MIM in firearms components. Additionally, designers have learned to take full advantage of design features like fillets, radiuses and ribs that add strength and durability without adding cost.”
Aerospace, medical, defense and automotive industries routinely use MIM products. Some car engines have rocker arms made by the process, and they take a beating thousands of times a minute. Magpul’s MVN35 likely brings that kind of performance in yet another critical piece of our EDC gear.